Metal Injection Molding (MIM)
Metal Injection Molding is an advanced manufacturing technology for the production of complex, high volume net-shape components with a high production rate. It introduced the plastic injection molding technique to powder metallurgy field and forms a new component manufacturing technique. As plastic injection molding is mainly used to produce complex and low price plastic products, metal powder is introduced to manufacture products of better intensity and durability. Such technique is called metal injection molding. So MIM technology combines the advantages of plastic injection molding and conventional powder metallurgy.
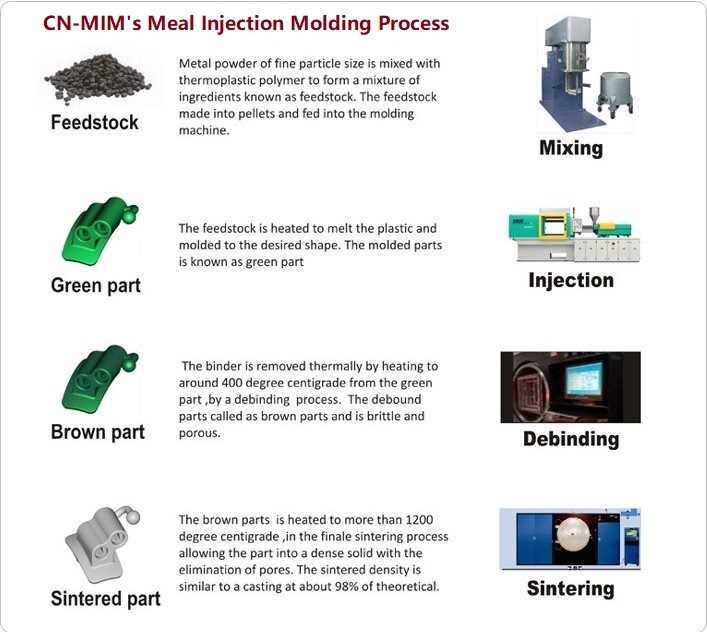
A MIM process consists of four steps: mixing, injection molding, debinding, and sintering. In the mixing step, a small quantity of a polymer with metal powder forms a feedstock that can be molded. After shaping, the polymeric binder system is extracted and the powder is sintered, often to near-theoretical densities.
Advantages
So what makes your part suitable for creation via MIM? To determine this, here’s a look at some of the advantages of the CN-MIM process:
Design Complexity: If you’re satisfied with the design freedom you get from plastic injection molding but want to craft metal parts, then MIM could be right for you. That’s because the two processes are quite similar in terms of design complexity – the main differences being that one produces plastic parts and the other metal ones. With MIM, cross holes, angle holes, splines, undercuts, side holes and grooves are all possible. Additionally, with MIM you can create whole parts that would often have to be created separately and assembled in post production.
- Small Size: Remember, MIM uses very fine powders to create fully dense metal parts. Hence, the process is best for small parts, typically those that weigh between 0.1 and 250 grams.
- Production Volume: MIM can be a very cost effective process, but only if the right number of parts are needed (not to mention if parts are the right size, as noted in the above point). Typically, the cost benefits are most noticeable and most worth it when part runs are between 10,000 and 20,000. Anything fewer than 10,000 and the potential cost savings from using MIM might not be evident at all.
- Properties: As we’ve already noted, MIM is able to create fully dense or near fully dense metal parts when the process is complete, if the process is carried out correctly. It’s particularly beneficial for parts that are too small or too detailed to machine out of bar stock. For comparison’s sake, it’s estimated that the part density is 98 percent via MIM, compared to 100 percent via conventional machining processes.
- Economical: Unlike machining, MIM doesn’t cut away existing metal – it uses only the amount of materials that is necessary to create the product. Nothing is wasted.
If your part meets some, if not all, of the above criteria, then MIM might be the production process for your part run. Talk with an CN-MIM specialist to learn what’s best for you. Now that we’ve covered the pros of the process, it’s time to next examine some of the cons of MIM.
Limitations
MIM isn’t a process for every part run. Talking with an A CN-MIM specialist will help you decide which process is right for you. Here are some of the process limitations you should be aware of:
Perhaps the largest limitation is the amount of post processing that may be necessary. For instance, one of the steps in the MIM process is binder removal, as in removing the excess binder that still exists on the metal material after it has been formed in the mold. The final part is roughly 20 percent larger than what it likely is intended, so there’s a lot of post-processing work involved. Additionally, that might not be even all the post-processing that’s needed. Aside from the sintering process, additional steps may sometimes be required, adding time to the process.
Another limitation is the cost. Not only is it necessary to create a mold, which adds to the up front costs of MIM, but any parts that are larger than 100 grams of weight can add further costs to part runs, which might not make it suitable at all for your product order. In fact, while MIM is ideal for smaller, more intricate pieces, it’s the opposite when it comes to larger metal pieces. If your product consists of a bigger product, MIM is probably not the right production method for you.
Design Considerations
We covered some of the design considerations in the “Advantages” section here, but it’s worth repeating. To recap, MIM is best utilized with part runs that are between 0.1 and 250 grams in weight – products that are larger are likely not worth the cost savings that you’re likely to save using MIM compared to other metal production technologies. Additionally, there are some other design considerations to consider, such as:
- Wall thicknesses of at least 0.15 mm.
- Wall thicknesses no larger than 12 mm.
Materials
The most common materials CN-MIM processes are iron, low alloy steels and stainless steels (such as Fe2Ni,304, 316L, 17-4PH). CN-MIM has many common variations of each to choose from.
Applications
MIM technology has been applied in various industries, such as the automobile, electronic, medical, hardware, aerospace, and defense industries.